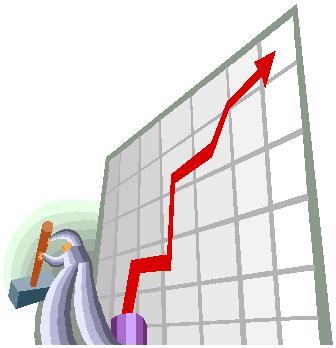
Définition de la TPM
Optimisation de la qualité des services et produits, réduction des coûts, meilleure flexibilité par rapport aux délais et rentabilité maximale, tels sont les objectifs de la TPM. Une technique de management qui, visant une amélioration permanente de l’entreprise, se base sur une meilleure gestion des ressources de production. Moyens humains et matériel sont les principaux acteurs de la TPM. N’étant pas un outil, ni une méthode de maintenance, cette forme de management requiert surtout une synergie entre tous les éléments, afin d’améliorer la performance des ressources internes, et ainsi atteindre une efficacité optimale. Cette performance se mesure par le Taux de Rendement Global ou "TRG", mis au point par le Japan Institute of Plant Maintenance ou JIPM en 1970.
Le TRG
Le TRG est le rapport entre la quantité de produits ayant pu être conçus dans les meilleures conditions et la quantité de produits de qualité fabriqués. Son calcul nécessite la définition des conditions idéales de production, notamment la performance exigée (temps de cycle, vitesse…) et le temps d’usage des ressources. Mis en place afin de mesurer la performance, le TRG se destine surtout au gestionnaire des ressources de production. Un TRG de 40% indique que la société n’a pas usé de toutes ses ressources, et qu’elle peut encore produire plus. L’investissement n’a été utilisé qu’à moitié, alors que le coût de revient inclut son amortissement sur sa valeur totale. La plupart des sociétés affichent un TRG de l’ordre de 40 à 60%.
Pertes de rendement : 16 causes détectées
Afin que l’application de la TPM soit efficace, il est nécessaire de déterminer les principales causes des pertes de rendement au niveau de l’entreprise. 16 facteurs ont été identifiés, et classés en 3 grandes catégories : la non-fiabilité des équipements, l’inefficacité des procédés et le manque d’organisation. La première famille inclut les pannes, les réglages en cours de série, les pertes de temps aux démarrages, les marche à vide et micro-arrêts, les retouches et rebuts, les sous-vitesses, ainsi que les arrêts programmés (nettoyage, réunion, inspection…). Les pertes relatives à l’inefficacité des procédés sont surtout dues aux surconsommations des matériaux et d’énergie. Le manque d’organisation concerne, quant à lui, les retards dans l’enchaînement des travaux, les temps de changements, les manques de savoir-faire et d’habileté, les temps de manutentions et de déplacements, les défauts de logistiques, ainsi que les excès de mesure.
Les 5 principes de base de la TPM
Ayant pour principal objectif une « performance économique de l’entreprise », la TPM se fonde sur 5 principes. Le premier met l’accent sur l’utilisation des équipements. Afin d’atteindre une efficacité maximale, il est nécessaire de respecter les conditions d’usage du matériel, d’éliminer le manque d’organisation, d’adopter des méthodes de prévention efficaces face aux défaillances naturelles et d’améliorer le savoir-faire des opérateurs. Le second principe de la TPM recommande un rapide démarrage des nouveaux équipements et produits. La démarche s’étale ensuite sur l’efficacité optimale des services, la maintenance des 5M (Matière, Milieu, Machine, Méthodes, MO) à haut niveau et la maîtrise de la sécurité et respect de l’environnement.